A fair amount of time has been spent since the last update, but it has been a 2 steps forward, one step backwards journey due to my seemingly endless stupidity....
So the last update left us with some inadequately formed bends in the test tube due to the jig crushing the tube. The first thing I tried was fitting a long 1/2" spring into the tube and trying again. This looked promising but was not quite there, probably because the tube ID is 14(ish)mm, and 12.7mm was not filling things up all that well.
I then bought a spring the next standard size up (standard for
Century Springs at least - these come from America, virtually the last bastion of what I shall kindly call an
antiquated measuring system), this spring had an OD of 14.3mm, but I figured quite rightly that it would wind into the tube without too much issue. I tried a couple of test bends which looked really good so I figured it was time to risk the real tubes - it was about now things started to go badly.
I had set up a smaller diameter tube to be the spring winding in and out helper, and this had a secondary function of measuring how far in the spring needed to sit to support the bend. I carefully measured this and wound in the spring, gingerly bent the tube and eagerly pulled it out to see the results - which was a completely crushed tube..... a bad word may have escaped my lips at this point.
Somehow I had managed to get the spring in the wrong position, carefully placed precisely 50mm away from the bend. What a tool. This was bad because the size of tube I had ordered was not a stock item and had to be shipped in from America - hence the 2 week wait. I now had precisely one good tube.
The next day I rang Lianne and asked if perchance she had ordered more of my tube - no she hadn't. She did however have quite a lot of tube with a smaller wall thickness - just over 0.7mm vs 0.9mm for the first tube. This should still be plenty strong enough so I ordered 2 lengths of that. This turned up the next day which was a result. I then bought a fresh spring, as the removal method of the old one had proved fatal to it's elastic limit - this may have had something to do with my state of mind as much as anything as I removed it.....
So today I set it all up again, very carefully checked the bend was in the right place, aligned in the jig etc, inserted the spring after checking it against my pencil marks on the tube and wrapping it with tape at the perfect insertion length, bent the tube.......... and got a bend that was halfway good and halfway crushed.
F________k.
(fill in the blanks, it will not be an intellectual stretch)
Somehow I had got the pencil markings for the jig alignment and for the bend proper mixed up and the spring was positioned only halfway along the bend. I genuinely do not understand how I could do that twice, maybe I am getting senile, which is eminently possible.. I bent the second tube just to prove that it was actually possible for a clearly retrograde intellect such as myself to achieve, and this turned out very well.
I shall ring Lianne on Monday.
Anyway, in between all this I started welding things, then cleaning them up;
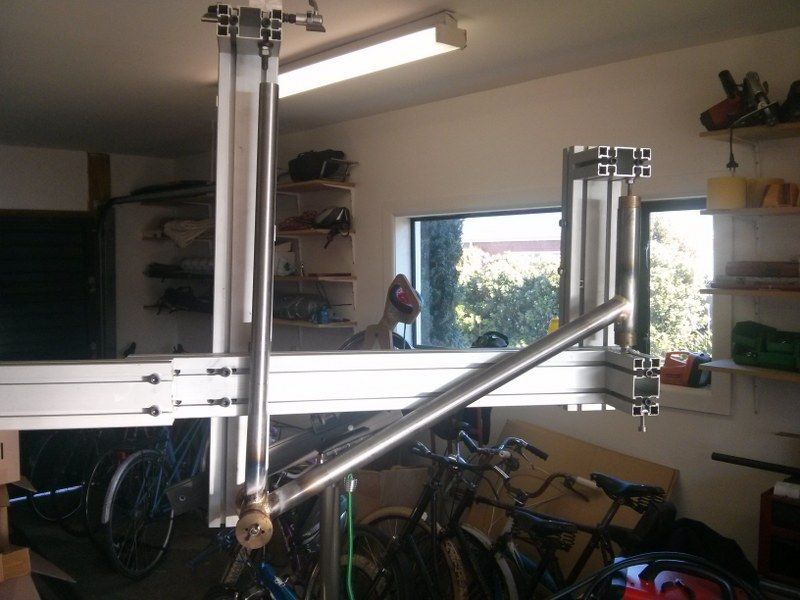 |
A wee bit of cold setting will be needed to straighten the seat tube |
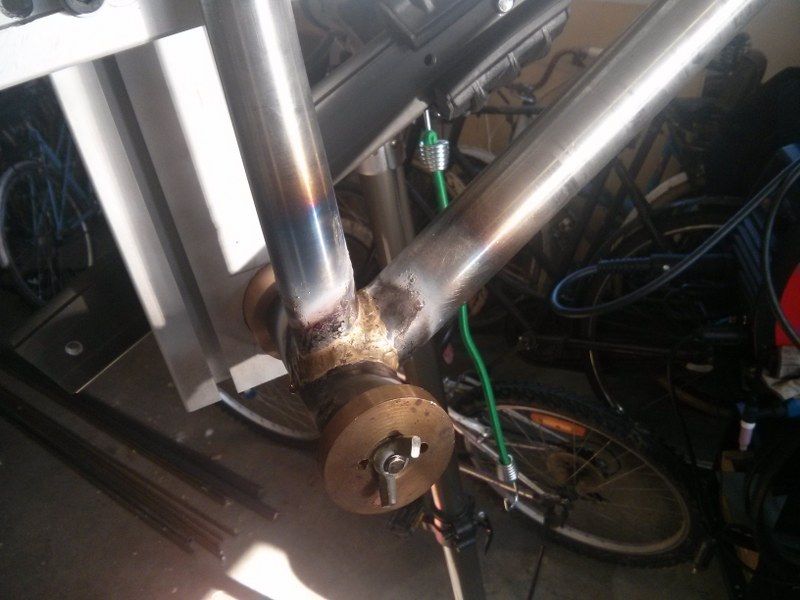 |
Raw welded tube |
 |
Raw welded tube, 2nd angle |
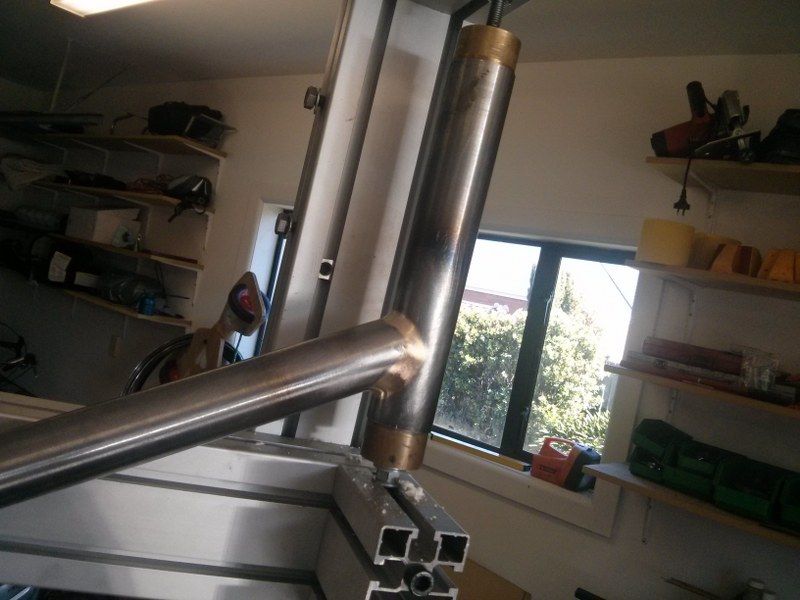 |
Mostly cleaned up head tube joint |
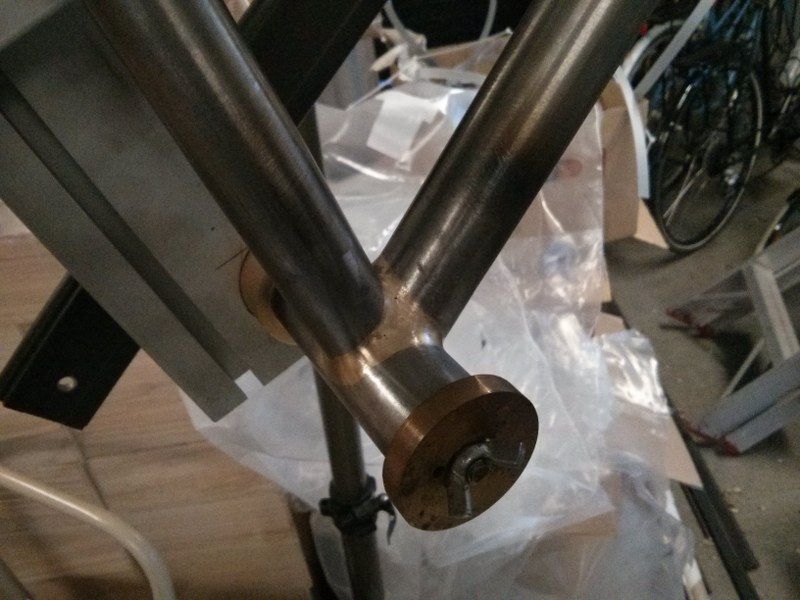 |
Mostly cleaned up head BB joint |
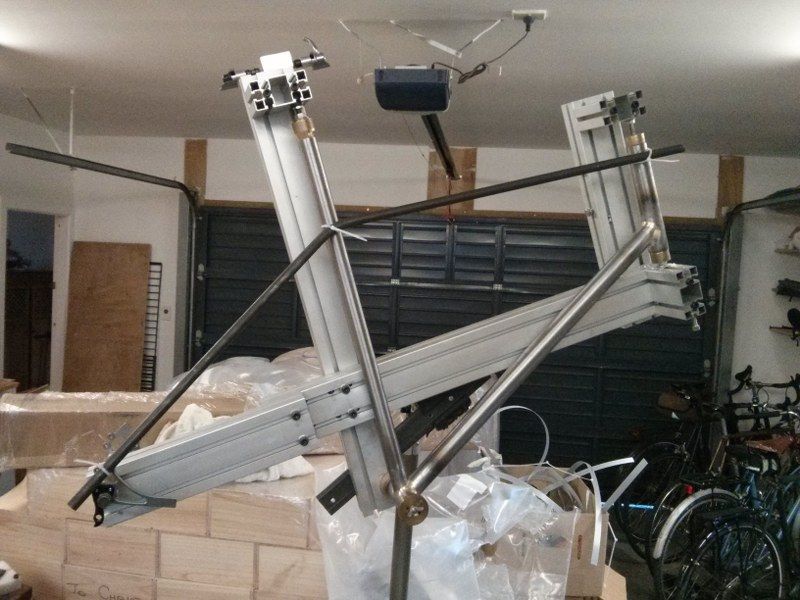 |
Sortof getting the idea... |
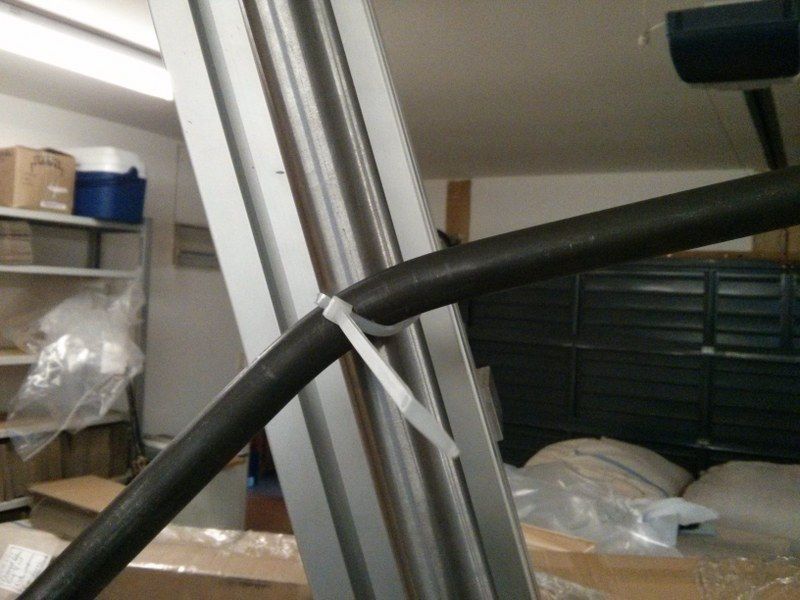 |
A single perfectly formed tube. |
The other big news is the
wheelset;
 |
My actual wheelset, today. |
My father had offered to pay for these, mostly because I asked him to. As I had decided it was an early Christmas present from him I did kind of use this as an excuse to go a bit further out there than I had intended. I therefore asked the extremely helpful Tristan from
WheelWorks to sort something for me and he appears to have done a sweet job. These have Fatbike specific Hope Fatsno hubs laced to Surly Rolling Darryl rims, mmmm tasty. These should be here tomorrow or Monday, I am gagging I can tell you.